Understanding CNC Machining Costs
Overview of CNC Machining
CNC Machining, or Computer Numerical Control Machining, is a subtractive manufacturing process that uses computer-controlled tools to shape a piece of material. This process is often contrasted with additive manufacturing processes, such as 3D printing. CNC Machining can create precise parts with tight tolerances, a key requirement in many industries.
Manufacturers often wonder why CNC Machining costs vary so much. A surprising story I remember is about a factory overseer who once saved his company thousands of dollars by simply adjusting the drill speed on their CNC machine, demonstrating the influence of even minor factors on cost.
General Factors Affecting CNC Machining Costs
Many factors contribute to the cost of CNC Machining, including the time taken, the skill level required, and the machinery used. For example, high-precision parts often require more costly machines, with more expensive maintenance costs. Consequently, a small change in any of these factors can significantly affect the overall cost.
Intriguingly, statistics show many manufacturers overlook these dynamics, leading to inefficiencies and unnecessary expenses.
Insights from Chinese CNC Machining Manufacturers
- Case Studies of CNC Machining Manufacturers in China
With an increasing number of businesses sourcing from abroad to cut costs, Chinese CNC machining manufacturers have become more relevant. These manufacturers have crafted strategic ways to reduce costs while maintaining quality.
A good illustration is the SparkFun Electronics case. This household name in the DIY electronics field owed part of its success to innovative cost-saving strategies adopted by its Chinese CNC Machining partner.
- Unique Cost Factors in Chinese Manufacturing
Manufacturing in China brings unique cost factors. For instance, Chinese manufacturers have pioneered methods to lower costs associated with energy consumption, labor, and materials.
One must also consider the investment in quality assurance that Chinese CNC machining manufacturers undertake to satisfy international standards. They often recruit bilingual engineers and invest in translation services to ensure clear communication with foreign clients.
- Predictions for Future Pricing
Given the evolving dynamics of the global economy, we can anticipate changes in CNC machining costs. Chinese manufacturing trends will likely have a considerable impact on global CNC machining costs.
An optimistic trajectory for the industry’s future lies in the fact that while the Chinese market is evolving rapidly, its manufacturers, especially the CNC machining manufacturers, are upskilling their workforce and leveraging advanced technologies to improve efficiency.
Overall, understanding CNC machining costs involves more than merely looking at the numbers. It requires an in-depth study of all contributing factors, including the process, machinery, and people involved. Thus, a focus on this knowledge is essential for the sustainability and profitability of manufacturing operations worldwide.
For deeper insights on any topic mentioned, thoroughly peruse related blogs and share your thoughts. We look forward to engaging with our community of readers in the comments section.
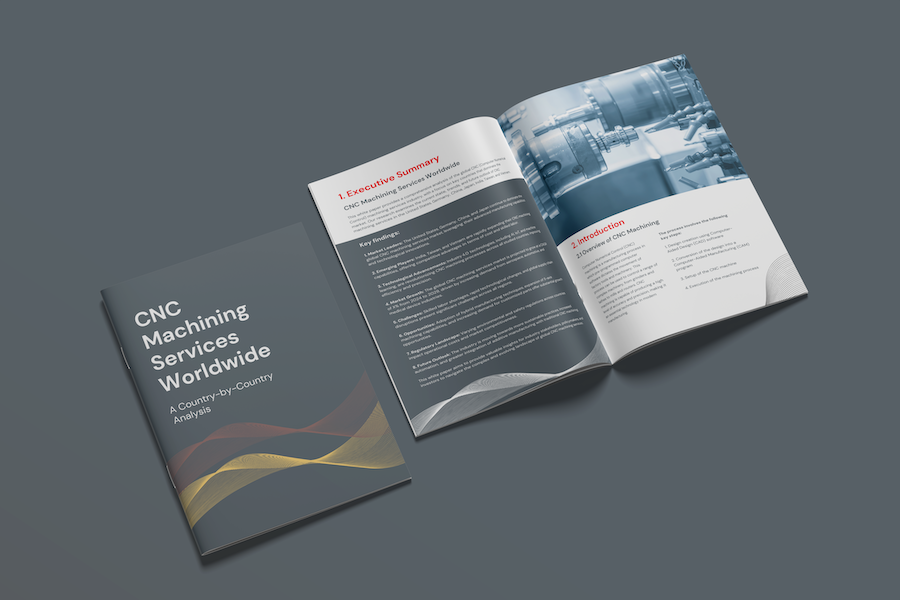
Download this comprehensive ebook on CNC machining services around the globe.
- comparative analysis
- market players
- technology advancement
- challenges
- opportunities
And it is absolutely FREE!
The American Procurement Journey – An Introduction
In the competitive world of faucet, shower head, and drinking fountain manufacturing, one American purchasing manager, John Thompson, Director of Procurement for a top-rated US brand, turned his sights eastward to China. His search mission was to find cost-effective, high-quality CNC machining manufacturers capable of meeting production demands.
Chapter 1: Recognizing CNC Machining Manufacturers
John understood that China is a global powerhouse when it comes to CNC machining manufacturers. Recognizing the potential for cost savings and efficiency, John decided to explore this opportunity.
The Research Phase
In his research phase, John learned about different CNC machining manufacturers in several Chinese cities. He made use of his strong analytical and networking skills to identify potential partners and extract relevant information related to costs, processes, quality, and scalability.
Chapter 2: Visiting Manufacturing Facilities
Impressed by what he found out about the CNC machining manufacturers, John embarked on his trip to China. He visited several facilities, examining their processes, evaluating their technology, and assessing their management structure.
Witnessing The Capabilities
During his visit, John observed modern, high-speed CNC machines in action at several CNC machining manufacturers’ processing plants, confirming their capacity and commitment to quality.
Chapter 3: Evaluating the Costs
Upon evaluating different CNC machining manufacturers, John discovered a significant difference in production costs as compared to American manufacturers. Cost-effectiveness being a prime consideration, John was inclined towards these manufacturers.
Digging Deeper into Costs
However, he was aware that these costs also included several factors, such as labor costs, material costs, equipment depreciation, energy costs, and more. John meticulously analyzed how these factors impacted the costs of CNC machining manufacturers.
Chapter 4: Decision-making Process
After considering his options, John decided on partnering with one of the reputed Chinese CNC machining manufacturers he had visited. This decision was based on their cost-effectiveness, technological proficiency, and overall readiness to meet his company’s demanding production schedules.
Finalizing the Deal
In finalizing his deal with the selected CNC machining manufacturer, John looked for potential ways of fostering a long-term collaborative relationship to yield mutual benefits.
The Key Factors Affecting CNC Machining Costs
- Material Costs
- The type of material used significantly impacts machining costs; metals like titanium and stainless steel are more expensive than aluminum or plastic.
- Material availability, market demand, and supplier pricing can also affect the overall cost.
- Part Complexity
- The more complex the design, the higher the cost due to increased machining time and required precision.
- Intricate geometries, tight tolerances, and multi-axis machining operations increase both labor and machine runtime.
- Production Volume
- Larger production volumes generally lead to lower per-unit costs due to economies of scale.
- Low-volume or custom orders tend to have higher setup costs and longer lead times, affecting overall pricing.
- Machining Time
- Longer machining times, especially for intricate or high-tolerance parts, drive up costs due to higher labor and equipment usage.
- Parts that require multiple passes, finishing, or slow cutting speeds also increase machine time.
- Setup and Preparation Time
- Complex setups, such as those involving multiple fixtures or programming, increase initial costs.
- First-time setups are more expensive, while repeat orders benefit from reduced setup times.
- Surface Finishing and Post-Processing
- Additional steps like polishing, anodizing, heat treatment, or painting add to the total cost.
- Complex surface finishes, coatings, or treatments that require more manual labor or additional machinery contribute to higher expenses.
- Lead Time
- Shorter lead times can result in higher costs due to expedited processing, overtime labor, and prioritization of resources.
- Machining providers may charge extra for rush orders to meet tight deadlines.
- Labor Costs
- The cost of skilled labor, including machine operators, programmers, and quality control specialists, directly affects machining costs.
- Labor-intensive processes, such as manual inspection or adjustments, further increase expenses.
- Location of the Supplier
- The geographical location of the CNC machining supplier influences costs due to factors like labor rates, transportation, and taxes.
- Sourcing from China often provides cost advantages, but shipping and customs costs may offset some savings depending on the destination.
These factors provide a detailed overview of the main cost drivers in CNC machining, helping to understand what contributes to the overall pricing from Chinese manufacturers.
Conclusion: The Journey Continues
John’s procurement journey serves as a significant example of the opportunities that Chinese CNC machining manufacturers provide. His story demonstrates that while factors affecting CNC machining costs do vary, a deep understanding of these factors can result in a mutually beneficial partnership between buyers and manufacturers.
Reference
1. China CNC Machining Services: Your Ultimate Guide
2. CNC Machining Certification Exam Guide – Setup, Operation, and Programming
3. Factors Influencing CNC Machining Costs