Understanding Common Quality Issues in CNC Machining China
CNC machining, or Computer Numerical Control machining, is a precision manufacturing process where computers control the tools and machinery. This technology has revolutionized production lines, making them faster, more efficient, and more accurate. In particular, the significance of CNC Machining in China is paramount, with the nation being a leading player in manufacturing, providing a high volume of goods to the global market.
However, like any manufacturing process, CNC machining in China is subject to a range of quality issues:
- Imperfect Finishing
Sometimes, products have imperfections in their finish, such as rough surfaces or irregular edges. These issues can affect the overall visual appeal and functionality of the product.
- Dimensional Inaccuracy
Precision is a critical aspect of CNC machining. Any mishap or error in measurements can lead to significant dimensional inaccuracies, rendering the part or product unusable.
- Erroneous Machine Readings
CNC machines function based on the digital instructions they receive. Any erroneous readings can lead to defects in the final product produced by CNC machining China.
- Issues with Machine Calibration
Machine calibration is vital for accurate production. If the machines are not properly calibrated, it may cause deviations in the final product’s dimensions.
- Material Waste due to errors
Inaccurate machining operations can lead to unnecessary material waste, escalating the production costs and negatively impacting the sustainability efforts.
- Software Glitches
CNC machines rely heavily on software to operate smoothly. Software glitches can cause operational disruptions, leading to poor quality output.
These common quality issues highlight the need for consistent, rigorous checks and implementing robust quality control measures.
Preventive Measures to Maintain and Increase CNC Machining Quality
In a bid to combat these quality issues in CNC machining China, several preventive measures can ensure quality consistency and enhancement.
Implementing Thorough Quality Control measures
The first and crucial step is implementing rigorous quality control measures.
- Routine Machine Maintenance and Checks
Regular maintenance and checks of the CNC machines ensure they remain at optimal working condition, reducing the risk of production disruptions and quality issues.
- Proper Calibration of CNC machines
Correct and regular calibration of CNC machines is vital for maintaining the quality of CNC machined products.
- Training Staff on Accurate Machine Operation
Having a well-trained staff who can promptly respond to and resolve any machine errors or malfunctions, or software glitches, can notably improve the product quality.
Utilizing Innovations and Technological Developments
Embracing new technologies can also significantly improve the overall product produced by CNC machining China.
- Advanced Software Applications for Precise Machining
Advanced software applications can provide a higher level of precision, thereby minimizing errors and defects.
- AI and IoT Use in CNC machines
The use of Artificial Intelligence (AI) and the Internet of Things (IoT) in CNC machines can lead to smarter, more efficient production, reducing errors and increasing output quality.
- Leveraging Robotics for Exhaustive Tasks
Integrating robotics into the manufacturing process can help perform labor-intensive tasks more effectively and accurately.
Reducing Material Wastage and Sustainable Practices
Material waste presents a significant cost to CNC machining, both economically and environmentally.
- Recycling and reusing material waste
Adopt initiatives to recycle and reuse material waste can greatly help in reducing the costs and promoting environmental sustainability.
- Optimization of CNC Processes
Optimizing production processes can minimize waste, enhance productivity, and boost the quality of final products produced by CNC machining China.
- Printing Evaluation and Error Detection
3D printing techniques help in performing pre-production evaluations to detect potential errors early and prevent material wastage.
Regular Training and Skill Development Programs
Continuous learning plays a critical role in maintaining high-quality output in CNC machining China.
- Workshop for Machine Operators
Organizing regular workshops for machine operators helps them keep up with the latest CNC machine operation procedures and maintenance routines.
Advanced Training on Newest Technological Innovations
Regular training on newest technological innovations will keep the staff updated, enabling them to operate the CNC machines efficiently and produce high-quality output.
- Importance of Regular Assessment and Continuous Learning
Continuous learning and regular assessments can ensure the staff’s skills and knowledge remain updated over time.
That concludes the journey of understanding common issues in CNC Machining and how preventive measures can not only maintain but increase CNC machining quality. By understanding the common quality issues, one can implement effective preventive measures to maintain and increase the overall product quality. That is the key to success in the competitive world of CNC machining.
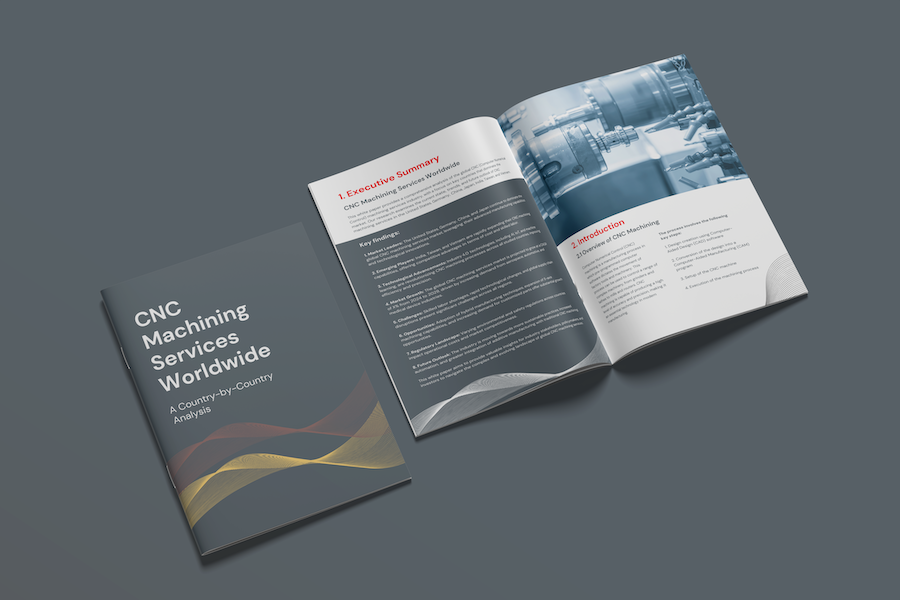
Download this comprehensive ebook on CNC machining services around the globe.
- comparative analysis
- market players
- technology advancement
- challenges
- opportunities
And it is absolutely FREE!
How to Prevent Common Quality Issues in CNC Machining China
Quality Issue | Description | Preventive Measures |
Imperfect Finishing | Rough surfaces or irregular edges affecting visual appeal and functionality. | Implement thorough quality control; use advanced finishing techniques. |
Dimensional Inaccuracy | Errors in measurements rendering parts unusable. | Proper machine calibration and routine checks. |
Erroneous Machine Readings | Incorrect digital instructions lead to defects. | Use updated software and conduct regular software checks. |
Issues with Machine Calibration | Poor calibration causing deviations in product dimensions. | Regular calibration of machines; operator training. |
Material Waste Due to Errors | Inaccurate machining causing unnecessary waste, increasing production costs. | Optimize CNC processes and integrate recycling and waste reduction methods. |
Software Glitches | Software malfunctions leading to production errors. | Use advanced, regularly updated software systems; conduct frequent updates. |
Structural and Assembly Issues | Faulty assembly causing structural weaknesses in products. | Implement rigorous quality checks at every stage of production. |
An American Journey to CNC Machining China for Plumbing Fixtures
In the ever-globalizing world of supply chain, John Smith, a well-established purchasing manager of a large American manufacturing company specializing in faucets, shower heads, and drinking fountains found himself looking to CNC Machining China for potential suppliers.
His journey began with a personal investigation on how to cut costs without compromising on quality. After thorough market research, he decided to source these products from reliable CNC Machining suppliers.
- CNC Machining China: Quality Problems Faced
As Smith embarked on the journey, he faced numerous quality issues. The initial CNC Machining China samples didn’t satisfy the tests for structural integrity and material quality. The issues ranged from inaccurate dimensions, inconsistent finishes, to faulty assembly.
- CNC Machining China: Lessons Learned
In his pursuit, Smith learned that the key to succeeding with CNC Machining is solidifying a strong partnership with the supplier. By communicating his needs and quality standards clearly, he was able to inaugurate a process of continuous improvement.
Navigating the CNC Machining China Landscape
The journey led Smith to visit various CNC Machining China factories. He discovered that implementing rigid quality control checks at every stage of production was vital. This scrutiny resulted in smoother operations and fewer faulty parts.
- Troubleshooting with CNC Machining China
Smith made several trips to CNC factories, working elbow-to-elbow with technicians and engineers to fix the quality issues. Monitoring the production process allowed Smith to catch errors early before they became costly issues.
- Collaboration with CNC Machining China
The partnership between Smith’s company and the CNC Machining China supplier strengthened over time. They learned to work synergistically, understanding each other’s strengths and weaknesses.
Conclusion: The Successful Outcome with CNC Machining China
The journey was not without its hiccups, but ultimately, seeking CNC Machining suppliers paid off. Smith’s company significantly reduced costs, improved quality, and built a stronger, more flexible supply chain. The story of John Smith is an example of overcoming obstacles in the pursuit of quality and cost-effectiveness with CNC Machining China.
Reference
2. Optimizing CNC Machining for Quality Production
3. Quality Control: Check Quality Early in the Manufacturing Cycle
4. CNC Machining Cost: A Guide on Influential Factors and Cost-Saving Strategies