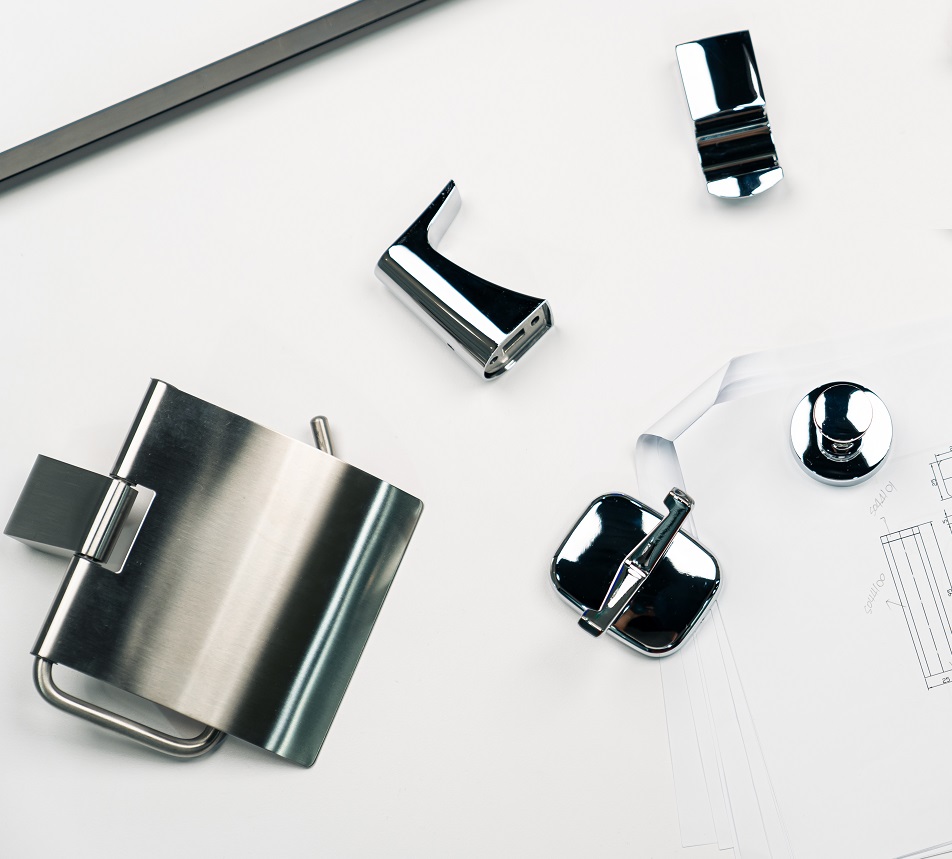
What is a Safety Faucet?
A safety faucet is a specialized type of faucet designed to prevent accidental burns and injuries by controlling the temperature and flow of water. Commonly used in environments where safety is a top priority, such as schools, hospitals, laboratories, and commercial kitchens, safety faucets are equipped with features like anti-scald mechanisms, tamper-resistant controls, and temperature limiters. These faucets ensure that water dispensed is at a safe temperature, protecting users from scalding and making them ideal for settings where vulnerable populations, such as children or the elderly, are present.
How Safety Faucets are Manufactured in Quantity
Manufacturing safety faucets on a large scale involves a combination of advanced engineering, high-quality materials, and stringent quality control processes to ensure each unit meets the rigorous safety standards required for their intended use. Here’s an overview of the process:
1. Design & Engineering
The production of safety faucets begins with meticulous design and engineering. Engineers use Computer-Aided Design (CAD) software to create detailed blueprints that specify the dimensions, materials, and safety features of the faucet. The design phase includes thorough testing and simulations to ensure that the faucet will perform reliably under various conditions and meet all relevant safety standards.
2. Material Selection
Given their critical role in safety, the materials used in safety faucets must be of the highest quality. Typically, manufacturers select corrosion-resistant metals such as stainless steel or brass, combined with durable polymers for certain internal components. These materials are chosen for their longevity, resistance to wear, and ability to withstand high temperatures.
3. Casting & Forging
The manufacturing process moves forward with casting or forging, where the basic components of the safety faucet are formed. In casting, molten metal is poured into precision molds to create the faucet body and other parts. Forging involves shaping the metal under high pressure, which enhances its strength and durability. These processes are highly automated to ensure consistency and efficiency in mass production.
4. Machining & Drilling
After casting or forging, the components undergo machining to achieve precise dimensions and a smooth finish. CNC (Computer Numerical Control) machines are used to drill holes, create threads, and refine the components to exact specifications. This stage is critical for ensuring that all parts fit together perfectly and that the faucet operates smoothly and safely.
5. Assembly
The assembly process involves carefully combining the various components, including the safety mechanisms such as anti-scald devices, thermostatic controls, and tamper-resistant features. This process is often automated for efficiency and consistency, though certain critical steps may require manual assembly by skilled technicians to ensure the highest level of precision and quality.
6. Calibration & Testing
Once assembled, each safety faucet is calibrated to ensure it delivers water at a safe and consistent temperature. This step includes setting the maximum allowable temperature to prevent scalding. The faucets are then subjected to rigorous testing, including pressure testing, leak testing, and functional testing, to verify that all safety features are working as intended and that the faucet meets all relevant safety standards.
7. Quality Control
Quality control is a crucial aspect of safety faucet manufacturing. Each unit undergoes thorough inspections to check for defects, ensure proper assembly, and verify that all safety features are functioning correctly. Faucets that do not meet the strict quality criteria are rejected or reworked to ensure that only the safest, most reliable products reach the market.
8. Finishing & Packaging
After passing all quality control checks, the faucets are polished and finished to achieve a smooth, attractive surface. Depending on the design, additional coatings may be applied to enhance durability and resistance to corrosion. The finished faucets are then carefully packaged with clear instructions for installation and use, ensuring they reach the end-user in perfect condition.
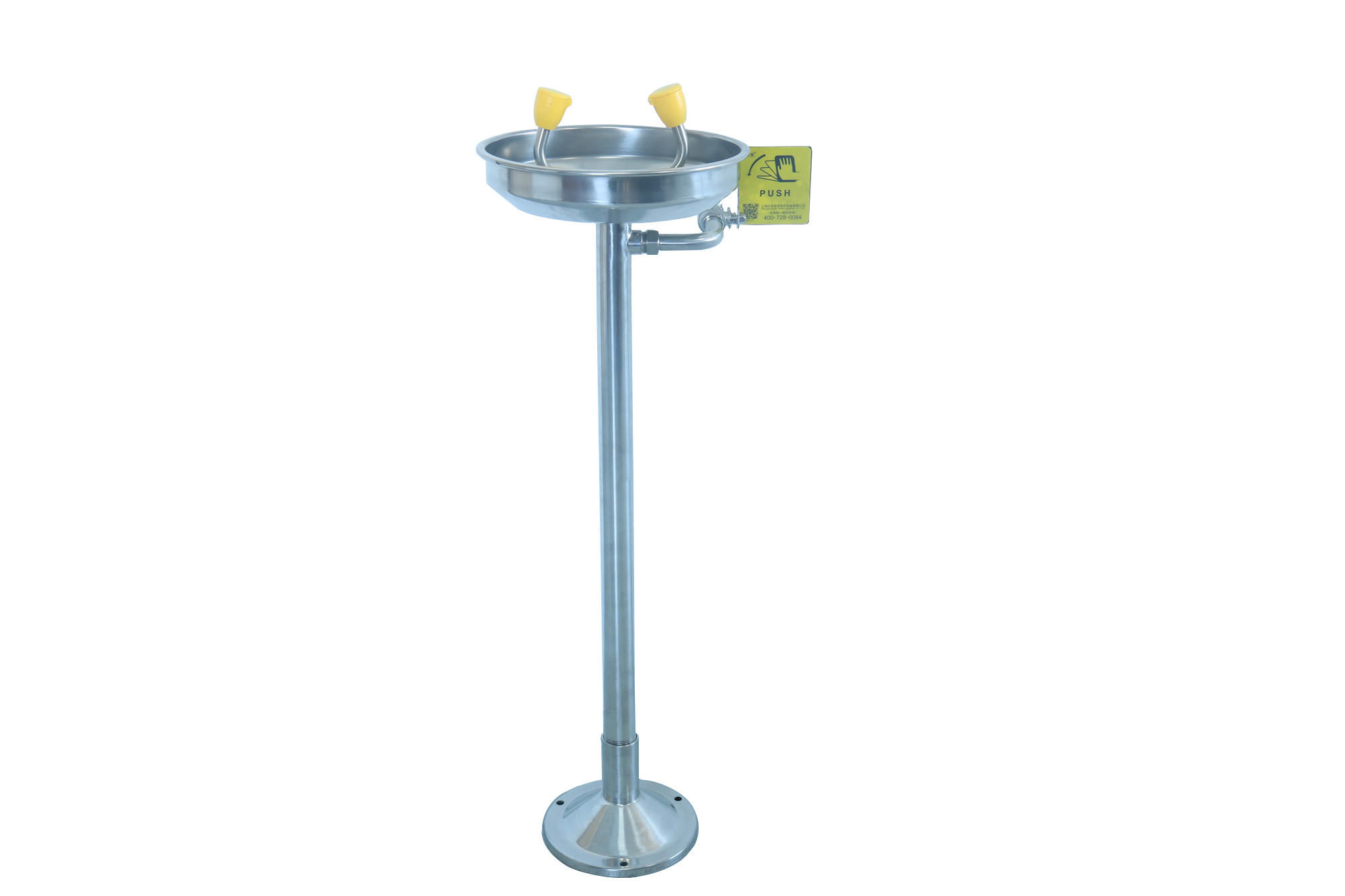