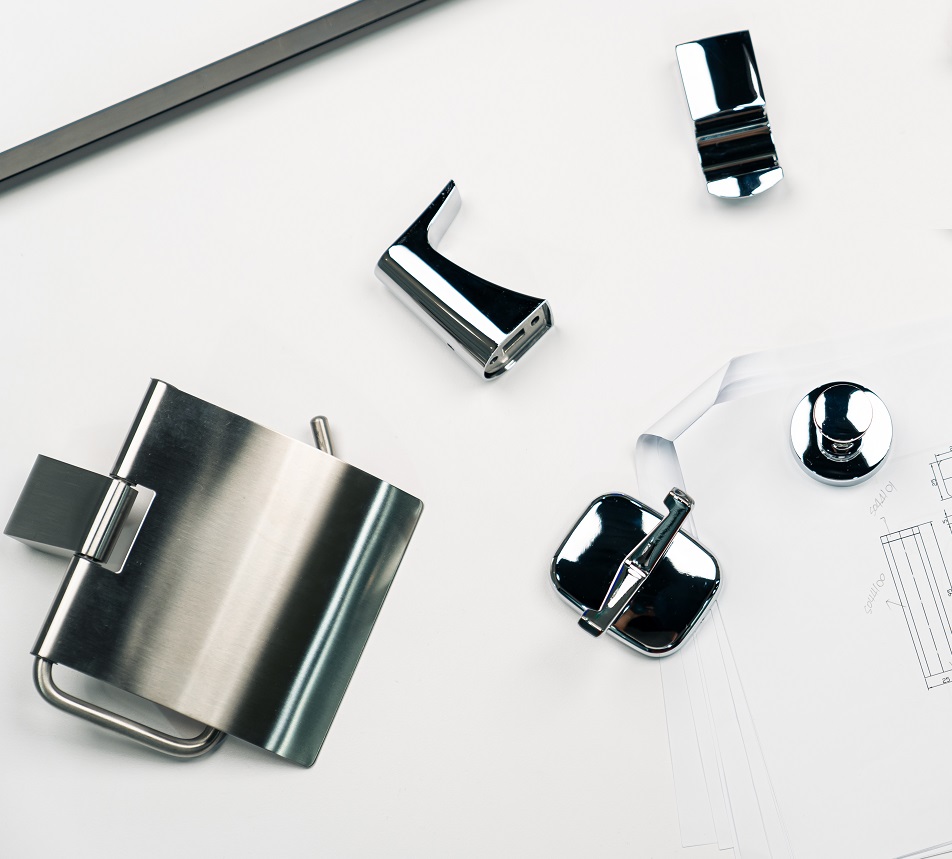
What is a Regulator?
A regulator is a crucial device used in various industries to control and stabilize the pressure or flow of gases and liquids within a system. Whether used in gas distribution systems, plumbing, industrial machinery, or HVAC systems, regulators ensure that the output pressure remains consistent and within safe limits, regardless of fluctuations in input pressure. This stability is essential for maintaining the efficiency, safety, and longevity of the equipment or processes in which they are installed.
Regulators come in different types, including pressure regulators, flow regulators, and temperature regulators, each designed to serve specific applications. They are vital components in systems that require precise control, such as gas welding, laboratory equipment, medical oxygen supplies, and fuel gas delivery.
How Regulators are Manufactured in Quantity
Manufacturing regulators on a large scale involves a series of highly controlled processes that ensure each unit meets stringent quality standards. Here’s an overview of how regulators are produced in quantity:
1. Design & Engineering
The process begins with the design phase, where engineers use advanced CAD (Computer-Aided Design) software to create detailed models of the regulator. These designs specify the exact dimensions, materials, and functional characteristics required for the regulator to perform reliably in its intended application. Rigorous testing and simulation are conducted at this stage to ensure the design will function correctly under various conditions.
2. Material Selection
The choice of materials is critical for regulators, as they must withstand high pressures and resist corrosion over time. Common materials include brass, stainless steel, and high-strength polymers. The selected materials are sourced from reputable suppliers to ensure consistency and durability.
3. Casting & Forging
For metal regulators, the manufacturing process often begins with casting or forging. In casting, the chosen metal is melted and poured into molds to form the basic shape of the regulator components. Forging, on the other hand, involves shaping the metal under high pressure, which increases its strength and durability. Both processes are automated for efficiency and precision, allowing for large-scale production.
4. Machining & Precision Engineering
After the initial shaping, the components undergo machining to achieve precise dimensions and smooth finishes. CNC (Computer Numerical Control) machines are commonly used in this stage to ensure each part meets exact specifications. Critical features such as threads, valve seats, and diaphragms are meticulously machined to ensure proper fit and function.
5. Assembly
Once all components are machined, they are carefully assembled. The assembly process involves fitting together various parts, including valves, springs, diaphragms, and seals, to create a complete regulator. Automated assembly lines are often used to increase production speed and maintain consistency, but certain high-precision models may require manual assembly by skilled technicians.
6. Calibration & Testing
Each regulator must be calibrated to ensure it maintains the correct pressure or flow rate under specified conditions. This step is critical for ensuring the regulator performs as expected in the field. Automated testing equipment is used to apply controlled pressure or flow to each unit, verifying that it meets the required performance criteria. Any units that do not meet specifications are adjusted or rejected to maintain high-quality standards.
7. Quality Control
In addition to performance testing, regulators undergo rigorous quality control inspections to check for any defects or inconsistencies. This includes visual inspections, dimensional checks, and leak tests. Quality control is integral to the manufacturing process, ensuring that every regulator that leaves the factory is safe, reliable, and meets industry standards.
8. Finishing & Packaging
Once they pass all quality checks, regulators may undergo additional finishing processes, such as surface treatments or coatings, to enhance durability and corrosion resistance. Finally, the regulators are carefully packaged to protect them during transit and storage. Packaging often includes detailed instructions and specifications to assist with installation and operation.
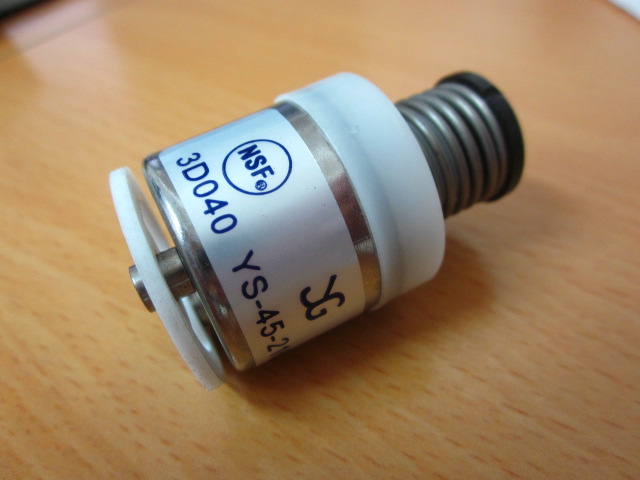