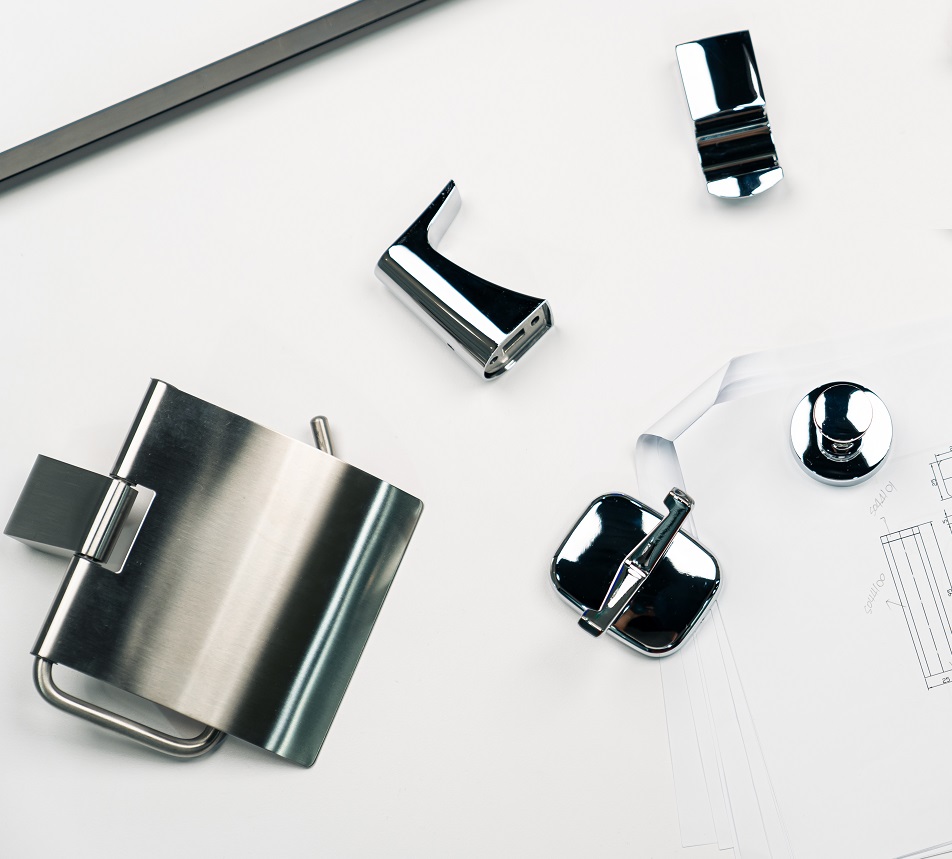
What is a Glass filler faucet?
A glass filler faucet is a specialized fixture designed primarily for commercial kitchens, restaurants, cafeterias, and other food service environments where quick and efficient filling of glasses, cups, or pitchers is essential. These faucets are typically mounted on countertops or sinks and feature a spring-loaded lever or push handle, allowing for easy one-handed operation. Glass filler faucets are known for their durability, ease of use, and ability to deliver a consistent flow of water, making them indispensable in high-traffic settings where speed and reliability are critical.
How Glass Filler Faucets are Manufactured in Quantity
Manufacturing glass filler faucets on a large scale involves a series of precise and controlled processes to ensure each unit meets high standards of quality, durability, and performance. Here’s a detailed overview of the production process:
1. Design & Engineering
The manufacturing journey begins with detailed design and engineering. Using advanced CAD (Computer-Aided Design) software, engineers create the blueprints for the glass filler faucet, specifying the dimensions, materials, and key features. The design is then subjected to rigorous testing and simulation to ensure it will withstand the demands of a commercial environment, including high usage frequency and exposure to varying water pressures.
2. Material Selection
Given the demanding environments in which glass filler faucets are used, material selection is crucial. Manufacturers typically use high-grade stainless steel or brass for the faucet body, which offers excellent durability, corrosion resistance, and a polished finish. Internal components such as valves and springs are also made from robust materials that can withstand repeated use without degrading.
3. Casting & Forging
Once the design is finalized and materials selected, the manufacturing process moves to casting or forging, where the basic shape of the faucet is formed. In casting, molten metal is poured into precise molds to create the faucet body and other components. Forging involves shaping the metal under high pressure to increase strength and durability. Both methods are used in large-scale production to ensure consistent quality and efficiency.
4. Machining & Drilling
After the initial casting or forging, the components undergo machining to refine their shape and ensure precise dimensions. CNC (Computer Numerical Control) machines are used to drill holes, create threads, and finish surfaces to exacting tolerances. This stage is critical for ensuring that all parts fit together perfectly and that the faucet operates smoothly.
5. Polishing & Finishing
To achieve the sleek, polished appearance that glass filler faucets are known for, the components are meticulously polished. Depending on the design, additional surface treatments such as chrome plating or brushing may be applied to enhance the faucet’s appearance and provide an extra layer of protection against corrosion. The finishing process is not only aesthetic but also functional, contributing to the faucet’s longevity in a busy commercial setting.
6. Assembly
The polished and finished components are then carefully assembled. This involves fitting together the faucet body, valves, handles, and other components. The assembly process may include installing seals and washers to prevent leaks and ensure a watertight fit. Automation is often used in large-scale production to maintain speed and consistency, though some high-end models may involve manual assembly by skilled technicians to meet specific quality standards.
7. Quality Control & Testing
Every glass filler faucet undergoes rigorous quality control and testing to ensure it meets the required specifications. This includes leak testing, pressure testing, and functional testing to ensure the faucet operates smoothly and reliably. Only faucets that pass these stringent tests are approved for packaging and distribution.
8. Packaging & Distribution
Once tested, the faucets are packaged in protective materials to prevent damage during transit. Packaging often includes instructions for installation and maintenance, ensuring that end-users can easily install and operate the faucet. The packaged faucets are then distributed to commercial kitchen suppliers, wholesalers, and retailers, ready to be installed in food service establishments worldwide.