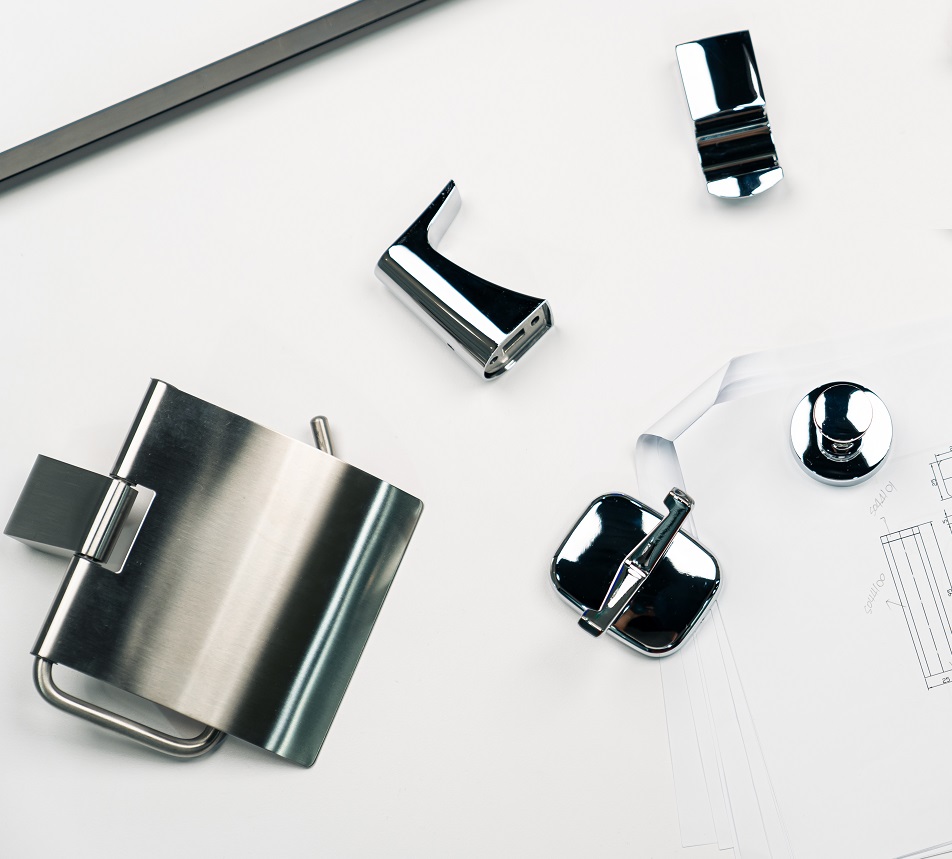
What is a Bubbler?
A bubbler, commonly found in public drinking fountains and water dispensers, is a small faucet designed to provide a steady stream of drinking water. It features a nozzle that directs water upwards in a controlled arc, allowing users to drink directly from the stream without the need for a cup. Bubblers are commonly used in schools, parks, gyms, and other public spaces where easy access to clean drinking water is essential. Designed for durability and ease of use, bubblers are built to withstand frequent use in high-traffic environments, making them an indispensable component of public hydration systems.
How Bubblers are Manufactured in Quantity
The mass production of bubblers involves a series of precise manufacturing processes to ensure each unit is reliable, durable, and meets health and safety standards. Here’s an overview of how bubblers are manufactured in large quantities:
1. Design & Engineering
The manufacturing process begins with detailed design and engineering. Engineers create precise CAD (Computer-Aided Design) models that specify the bubbler’s dimensions, material composition, and functional features. The design phase includes extensive testing and simulations to ensure the bubbler provides a smooth, consistent water flow while being resistant to wear and corrosion.
2. Material Selection
The materials used in bubblers are selected for their durability, safety, and resistance to corrosion. Stainless steel and brass are commonly chosen for the main body of the bubbler due to their strength and longevity. For the nozzle and other water-contact parts, materials that comply with drinking water safety standards are used to ensure the water remains clean and uncontaminated.
3. Casting & Forging
Once the design is finalized and materials selected, the manufacturing process moves to casting or forging. These processes involve shaping the bubbler’s components from molten metal. In casting, the metal is poured into molds to form the basic shapes of the bubbler parts. Forging, on the other hand, involves applying high pressure to shape the metal, enhancing its strength and durability. Both methods are automated to ensure consistency and efficiency in high-volume production.
4. Machining & Drilling
After casting or forging, the bubbler components undergo machining to achieve precise dimensions and a smooth finish. CNC (Computer Numerical Control) machines are used to drill holes, create threads, and refine the nozzle shape to ensure a consistent water flow. This step is crucial for ensuring that all parts fit together perfectly and that the bubbler functions correctly.
5. Polishing & Finishing
To ensure a sleek and sanitary finish, the bubbler components are polished and may receive additional surface treatments, such as chrome plating or electro-polishing. These finishes not only enhance the bubbler’s appearance but also add a layer of protection against corrosion and wear, ensuring the bubbler remains in good condition even after prolonged use.
6. Assembly
The assembly process involves carefully combining all the bubbler’s components, including the body, nozzle, and any internal mechanisms that control water flow. This stage is often automated to maintain production speed and consistency. However, certain high-end models may require manual assembly by skilled technicians to ensure the highest quality standards are met.
7. Quality Control & Testing
Quality control is a critical part of the manufacturing process. Each bubbler is subjected to rigorous testing to ensure it meets both performance and safety standards. Tests include checking for consistent water flow, verifying the integrity of seals to prevent leaks, and ensuring that the materials used are free from harmful contaminants. Bubblers that do not pass these tests are either reworked or rejected.
8. Packaging & Distribution
Once the bubblers have passed all quality checks, they are packaged for distribution. Packaging is designed to protect the bubblers during transit and may include instructions for installation and maintenance. From there, the packaged bubblers are shipped to distributors, retailers, and end-users, ready to be installed in public spaces where they will provide clean, accessible drinking water.
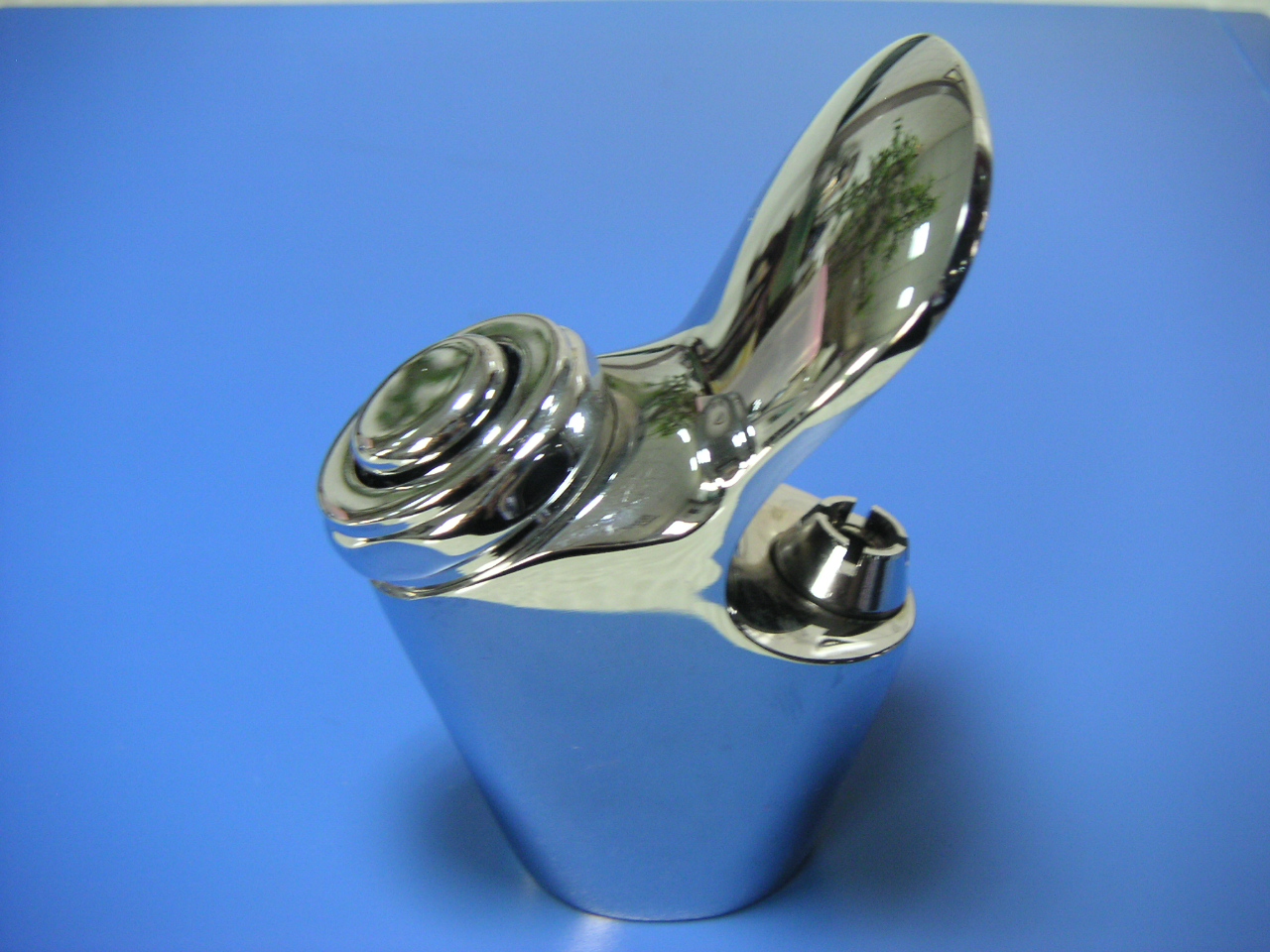